
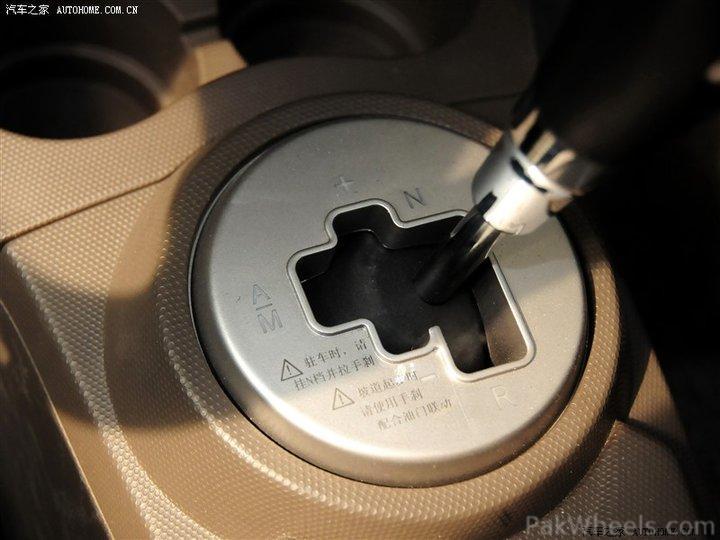
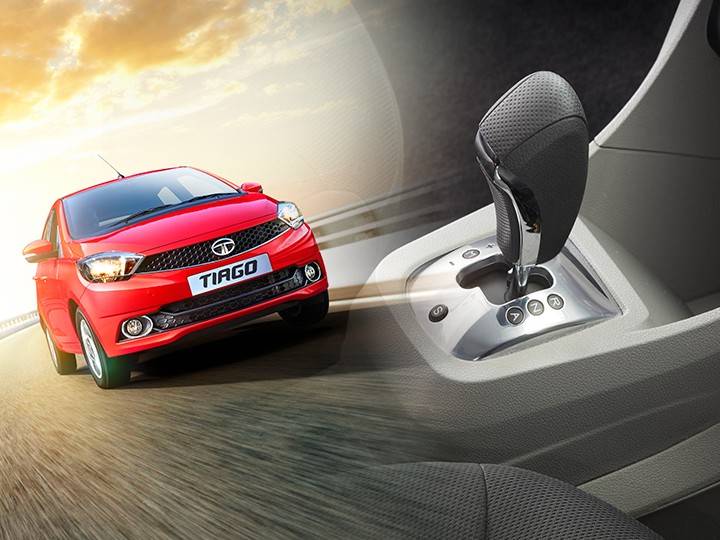


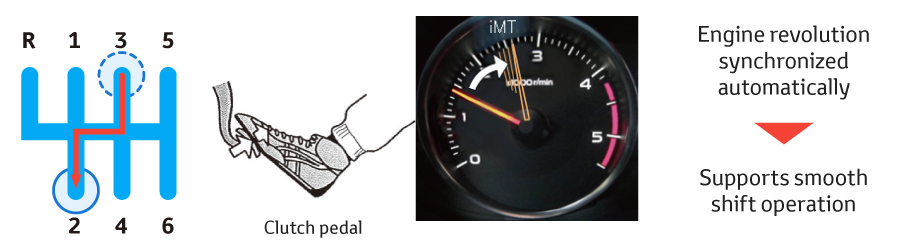
cars with Automated Manual Transmissions (AMT) for gear shift control offer many advantages in terms of reduction of fuel consumption and improvement of driving comfort and shifting quality.


Essentially, the AMT is nothing like the conventional auto boxes. It operates on the manual transmission of a car just like a driver would.


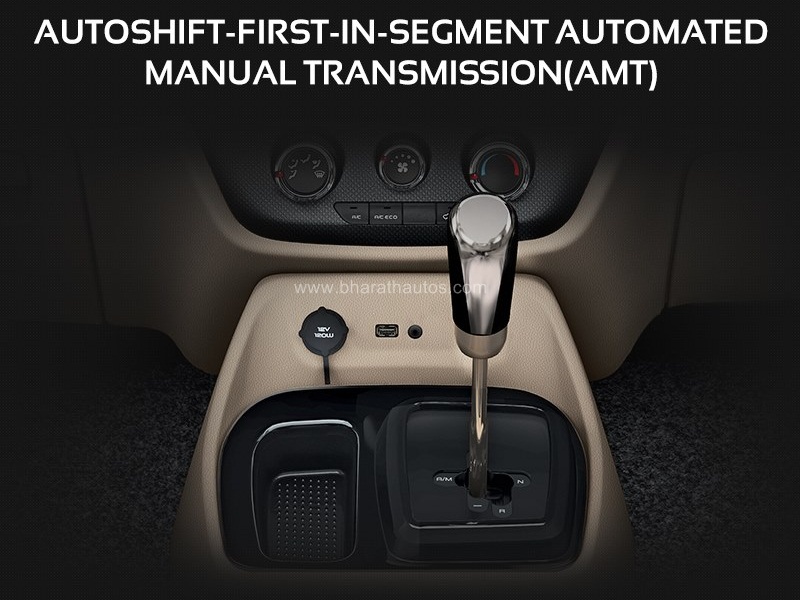
Clutch Systems
The Manual Transmission Has a Future
E-Clutch and Hybridization
I. IntroductionI. Introduction
In view of an increasing variety of transmission concepts, the manual transmission continues to be one of the most important transmission designs. Worldwide, 43 % of all car buyers order their new car with a manual transmission. Most manual transmissions are sold on the Indian subcontinent, but they are also very popular in Europe and China. Although the percentage of manual transmissions will decrease slightly over the next few years on a global scale, the upward trend will continue in a growing market when measured in absolute production quantities. According to market observations by Schaeffler, the number of manual transmissions produced worldwide, which amounted to 40 million units in 2016, will continue at its current high level.
There are distinct regional differences. While, based on these assessments, the market share in India will be at 90 % in 2025, it will reach 57 % in Europe, 51 % in Southeast Asia and 45 % in China [1]. The major reasons for the popularity of manual transmissions in these markets are a comparatively low price in combination with very high efficiency. For a long time, manual transmissions were superior to automatic transmissions in terms of fuel consumption. Then, however, automatic transmissions used optimized gearshift curves and were able to achieve advantages in driving cycles compared to the predefined shifting points for manual transmissions. These consumption benefits were primarily made possible by down-speeding, supported by continuously improved torsional vibration dampers and, in torque converter transmissions, by closing the lock-up clutch at a much earlier stage [2, 3]. Under real driving conditions and with carefully selected shifting points, manual transmissions can further demonstrate their efficiency benefits.
In order to use the opportunities offered by new technologies to reduce fuel consumption and CO₂ emissions, it is necessary to automate the clutch in manual transmissions. For instance, achieving fuel-saving driving strategies such as coasting with the engine turned off or the recuperation of braking energy with 48 V hybrid systems in P0 or P1 arrangement is neither comfortable nor feasible without the driver’s assistance unless an automated clutch is used.
In view of global climate goals, the utilization of this potential is extremely effective because, as shown above, the worldwide usage of manual transmissions will continue. Using a coasting-only strategy can achieve fuel and CO₂ savings of 3 % to 5 %, and the expanded recuperation of braking energy with mild hybrids can reach around 5 % and, when combined, around 8 %. This paper aims to show solutions designed by Schaeffler that follow this approach and enable the automation of manual transmissions for more efficiency and reduced emissions.
II. Automated clutch actuation
Initial situation
Coasting with the engine turned off and the recuperation of brake energy with 48 V hybrid systems in a P0 or P1 arrangement require optimized clutch actuation. Since the driver usually is not able to perform this operation, automation of the clutch becomes mandatory. When coasting, the primary objective is to open the clutch at the right time so that the engine continues to idle at low speed or, even better, can be turned off altogether. In hybridization, the automated clutch is useful for disconnecting the internal combustion engine and the electric motor for coasting, according to the current traffic situation and driving strategy, or for connecting a fuel overrun cut-off to support recuperation.
An automated clutch can also be used to implement additional functions in a simple way. For instance, it permits extended assistance functions such as the traffic jam assist that carries out starts and stops in slow-moving traffic on the interstate. Other functions are the protection of the clutch and the powertrain from excessive loads, such as in case of misuse, and the increased safety of vehicles and passengers. One example here is the automatic opening of the clutch when the assistance system initiates an emergency brake application to prevent the engine from stalling.
Implementation variants of the automated clutch
MTplus is an entry-level system for the partial automation of the clutch that is below the technical level required for CbW and ECM systems [4]. An actuator with a suitable design is used in addition to the existing master cylinder on the clutch pedal. This actuator, whose functional principle is described in more detail in the following chapter, has a time interval of 300 ms to open the clutch, providing sufficient dynamics for the basic function of entering and exiting the coasting mode. One challenge was to find an actuator concept that would permit conventional and automated clutch actuation at the same time. This is because on the one hand, the actuator must not interfere with normal foot actuation and on the other hand, the driver must be in control at all times.
CbW are perceived as normal manual transmissions with a clutch pedal by the driver. The strength of the mechanical pedal resistance, however, is “simulated” by means of a force emulator. A travel indicator recognizes the pedal position and reports it to a control unit. The actual actuation of the clutch is carried out by an actuator. As the name “by wire” suggests, there is neither a mechanical nor a hydraulic connection between the clutch pedal and the slave cylinder of the clutch. That is why the performance of the system depends on the actuator. The new hydrostatic or mechanical Modular Clutch Actuator (MCA) developed by Schaeffler reaches time intervals of just 150 ms for opening the clutch, allowing additional functions such as the start assist, the traffic jam assist and driving dynamics features such as slip control. This actuator is described briefly in the following chapter.
ECM systems do entirely without a clutch pedal. Instead, a sensor on the gear selector recognizes the intent to shift gears. In the past, LuK already volume produced automated clutches as two-pedal systems, such as the BMW Alpina (1993) and the Mercedes-Benz A Class (1997). At the time, however, the efficiency potential of electrified vehicles and modern driving strategies was not available. That is why the systems were not successful on the market.
MTplus actuator function
Figure 2 Operating conditions of the actuator: Clutch actuation by driver and pedal, actuation by actuator only when coasting and return to actuation by the driver
The cross-section shows the electric motor with the spindle drive and the connections to the master and slave cylinder. In normal operation, the master cylinder is actuated hydraulically (yellow arrow in figure) through the open ventilation hole with a connection to the clutch pedal, and the actuator is disabled. When coasting, the actuator moves a split piston (depicted in blue in the figure) forward via the screw drive and the spindle, interrupts the hydraulic flow from the pedal and actuates the slave cylinder directly to open the clutch. However, if the actuator is now in coasting mode and the driver wants to take control, the idea is for the driver to feel a pedal curve similar to the one in normal operation, even though the clutch has already been opened by the actuator. That is why the hydraulic fluid is transferred to a cache piston in the actuator and pressure is built up when the clutch pedal is actuated. Simultaneously, a sensor on the pedal informs the actuator that the driver wants to take control. When stepping on the pedal, the driver feels a counterforce that is generated by a spring intended for this purpose (depicted in red in the figure). Starting at a specified point, the pressure in the cache piston and the pressure on the clutch side are compensated. The rear part of the piston now moves back and frees up the channel with the hydraulic fluid which takes control of the front part of the piston. The clutch remains open throughout this process. This change in slave cylinder control implemented in this way goes unnoticed by the driver.
Clutch actuator
Figure 3 Schaeffler’s modular clutch actuator (MCA)
The drive unit of the actuator can be designed in three variants: Hydraulic with or without an integrated reservoir or mechanical with a tappet that actuates the clutch lever directly. The integrated power and electronic control unit contains five sensor inputs for additional sensors, and the driving strategy is represented by the software. The compact and robust design allows the actuator to be installed right on the transmission in the engine compartment, making it a plug-and-play solution at the plant that is manufacturing the vehicle. Schaeffler has equipped several test vehicles with this system, and start of production is scheduled for the end of 2018.
Functions of automated clutches
Figure 4 shows the most important functions of the implementation variants for automated clutches. Generally, the functions are divided into three groups that are of varying relevance to drivers.
Figure 4 Functions of the automated clutch in the MTplus, CbW and ECM variant
The functions affecting start/stop and coasting are especially important to automobile manufacturers because they can be instrumental in reaching CO₂ fleet goals. In the figure, they are referred to as “coasting and efficiency”. The second group, “comfort and driving pleasure”, by contrast, are primarily important from the customer’s point of view because of the functions shown here, such as a park assist system that customers can experience firsthand – and will buy. The third group refers to “robustness and safety”. This is what car buyers take for granted.
III. Development of driving strategies
Development and evaluation method
One of the elements used by Schaeffler to analyze potential implementation variants for the coasting functions is an RDE-compliant track around the company’s Bühl location and consistent testing conditions. The consumption measurements taken here are an important basis for the development and design of coasting strategies for automated clutches.
In a field test by Schaeffler on the design of a passive coasting function, which is described below, a total of 42 test drives were performed by four different vehicles on the RDE-compliant test track. Half of the drives (21 cases) included coasting mode, while the other half did not use coasting. The test drives were completed by a total of nine different drivers to allow a better analysis of driver influence.
Figure 5 Field test on coasting mode: Video material synchronization with measured data
No comments:
Post a Comment